Servicing the Valley of the Sun
Phoenix • Scottsdale • Peoria
We Replace Old Water Heaters
- SAME DAY SERVICE -
6 am to 7 pm Mon-Sat
Legionnaires' disease | Water Heater Pros | Sacramento, Ca
What is Legionnaires Disease

LEGIONNAIRES' DISEASE AND WHY?
Legionnaires' disease, or Legeionellosis, is caused by "Legionella pneumophila, a ubiquitous aquatic organism that thrives in warm environments." It was identified after 34 Veterans died after attending an American Legion Convention in the Bellevue-Stratford Hotel in Philadelphia in 1976.
This is a type of pneumonia caused by bacteria. You usually get it by breathing in the mist from hot water that contains the bacteria. The mist may come from bathtubs, showers, hot tubs this bacteria can be found in water heaters where low HEAT temperatures are present.
Installing a master mixing valve on a domestic hot water system adds an extra layer of safety.
By Rick Cota and Eric Costa
Leonard Valve's Nucleus digital mixing valve provides complete system monitoring with outlet temperature control within +/- 2° F from setpoint, regardless of demand.
Hot water has been around since man first harnessed the power of fire, but when at elevated temperatures, it is dangerous and even deadly. Today’s hot water heaters offer a diverse range of technologies that perform leaps and bounds ahead of their predecessors, but what temperature should they deliver? Some facilities may simply set the heater to a usable temperature, but while this may seem like an acceptable practice, there is an issue that needs to be addressed: Legionella.
One of the biggest concerns for hot water systems in commercial buildings is Legionella bacteria. Legionella is a bacterium that enters the human body by inhalation and aspiration of water droplets, and is responsible for Legionnaires’ disease, a bacterial infection of the lower respiratory system that often gets misdiagnosed as pneumonia; one in 10 people who contract Legionnaires’ disease will not survive. Below is a Legionella Growth Chart, which shows the bacteria growth behavior. These organisms live and multiply in water between 68° F and 122° F and thrive in water 95° to 115°. At 121°, Legionella bacterium stops multiplying but is still present in water.
There are many ways to combat Legionella in a domestic hot water system. UV light treatment is a method used to treat bacterial removal; however, additional heat is the most common method. Since the first clinical study was done in 1977 by the Allegheny County Health Department, more and more commercial water heater systems are heating to temperatures above 140° to kill the bacteria. Since then, the plumbing design industry generally follows the ASHRAE 2000-12 guideline, which suggests thermal disinfection by sending hot water 165° to 175° through the domestic hot water system.
These higher temperatures, while necessary, pose a scald danger for end users. This is where a master mixing valve becomes extremely valuable. A master mixer is regularly used to reduce the temperature down to a more usable area (between 124° to 130°), and then circulated throughout the building. A portion of the return water from the domestic hot water line is sent back to the hot water source to be reheated, which helps keep Legionella growth in check.
Master mixing valves provide a buffer between the high-temperature heat source and endpoint fixtures. Hand washing faucets in public restrooms will typically have hot water supplied from a small point-of-use mixing valve. The presence of these valves will tempt designers and contractors to skip the installation of a master mixing valve. While this does work initially, the building is at a higher risk of scalding end users since these small valves are often forgotten and not well maintained. Over time, these valves will fail and potentially allow “full hot” through them. If “full hot” is 140° or above, the risk of scald is significant. By installing a master mixing valve, “full hot” is tempered down to the fixtures keeping a set temperature safe for end users. For reference, below is a water burn chart so that the danger can be fully appreciated.
Master mixing valves also keep domestic hot water temperatures consistent, even with large inlet temperature changes. As part of the ASSE 1017 certification, all master mixers must control the outlet temperature within a specified range from the initial set point when there is a 25° increase to the hot water inlet temperature. The allowable variance can range from ±3° to ±7°, depending on the size and flow rate. Most thermostatic master mixers hold to within ±3°, and digital master mixing valves are known to hold within ±2°. Without a master mixing valve, a large increase in hot water temperature can be a dangerous situation.
Pressure-balanced shower valves are of particular concern since they do not offer thermal protection; large increases to the domestic hot water temperature will be directly felt by the end user. If a master mixing valve is installed, the large increase in hot water temperature from the heat source is tempered down and end users are better protected.
Energy and cost savings are other benefits of installing a master mixing valve. Instead of having to heat 100% of the hot water needed for the building, the heater is only needed for a fraction of that when a master mixer is present in the system. Consider a system that requires a domestic hot water temperature of 125°. If the hot water supply is set to 140° with a mixing valve installed downstream, 83% of the volume needs to be heated, assuming the cold-water temperature is 50°. At 160°, only 68% of the domestic hot water needs to be heated.
This reduction will save the facility energy and the system becomes environmentally friendly. In addition, since the heaters are heating a lower volume of water, a smaller unit may be sufficient, and wear and tear to the heater and related equipment is reduced.
Installing a master mixing valve on a domestic hot water system is simply good practice. They add an extra layer of safety to any system. Having a master mixer allows facilities to heat and store water at elevated temperatures, which kills Legionella bacteria while delivering safe hot water temperatures for multiple applications. If a heating system malfunctions and a large increase in the hot water temperature is seen, a master mixing valve will flatten the spike to the domestic hot water system. The inclusion of a mixing valve will also save energy and lengthen heater equipment service life.

Best Practices for Legionella Mitigation
Rising Legionella outbreaks underlay the need for better plumbing design, mitigation efforts
There’s no doubt the plumbing industry has had a hyper-focus on Legionella and prevention over the past few years. Yet a simple search on Google reveals outbreaks in an Illinois prison, a Hawaiian hotel and in Riverside County, California — all within the the last quarter of 2022.
“As bacteria is formed and spread through water, the older America’s water infrastructure becomes, the chances for Legionella outbreaks increases, especially in states that have warmer climates,” such as Arizona, explains Matt Sigler, PMG Executive Director for the International Code Council (ICC). “A common way the bacteria forms is through lukewarm water temperatures as it thrives in water that ranges from 78°F to 119° F, making it a potential breeding ground for the bacteria.
Additionally, water that is stagnant within a piping system runs the risk of having disinfectant dissipate, inviting the potential growth of Legionella bacteria.”
Legionella is still very much present — and abundant — in today’s buildings, according to Bruce Fathers, senior product manager for Watts a major plumbing
products manufacturer in the USA.
“A facility manager’s ability to fully eliminate the risks of this bacteria has a lot to do with proper system design and water management,” he says. “Another thing to consider is that buildings may be renovated or enlarged — work that can greatly impact a plumbing system’s susceptibility to Legionella. Building renovations are often one of the leading causes of plumbing system dead legs — when piped systems are altered, they can create unforeseen problems. Also, maintenance schedules cannot be ignored. This can happen during staff turnover.”
Fathers notes that there is also a tendency among facility managers to save energy by reducing water storage or distribution temperatures, which can allow bacteria growth. “Another condition ideal for opportunistic bacteria growth are the use of low-flow plumbing fixtures,” he adds. “Not long ago, fixtures may have been rated at 2.5 gpm. Driven by water conservation efforts, the popularity of fixtures with ratings of 0.25 gpm to 1.5 gpm, Legionella bacteria can prosper in slower-moving distribution piping runs, protected by insulative biofilm.”
The plumbing industry is more aware, especially in health care facilities, of the risks associated with Legionella which has led to increased surveillance of the disease, says Special Pathogens Laboratory (SPL) Consulting Services Vice President Dave Pierre, who is also an ASSE-certified Legionella Water Safety and Management specialist.
“Legionnaires’ disease has always been underdiagnosed, so the increased awareness has led to us doing a better job at identifying cases of disease,” he explains. “Additionally, we have a lot of aging infrastructure, ongoing construction and renovation of buildings. We know these events and conditions can increase the nutrients in the water for Legionella and other waterborne pathogens to proliferate. Also, globally, we have increasing source water temperatures which leads to a more suitable environment for Legionella to grow. The last piece of the puzzle is our aging population. As our population ages, we have more people falling into our ‘at-risk’ groups, including growing elderly and immunocompromised populations. Did you know that the risk increases at the young age of 50?”
Water safety is key to prevention
While cases of Legionnaire’s disease have increased nine-fold between 2000 and 2018, John Lansing, plumbing designer for Portland, Oregon-based PAE Engineers, notes there is still very little oversight and regulation regarding Legionella.
“When I say Legionella, I mean specifically Legionella mitigation practices in the building water systems,” Lansing says. “And while Legionnaires’ disease cases have increased on an international level, it’s significantly less pronounced in other countries. For example, the United Kingdom has some of the lowest cases of Legionnaires’ disease in the world. It’s still a big problem, just not to the extent it is here in the U.S. It really comes back to how important Legionella mitigation practices are — that’s something the UK has shown leadership with. The Chartered Institute for Building Service Engineers (CIBSE) in the UK published TM13 back in 1987 after the Stafford District Hospital Legionnaires’ disease outbreak. TM13 is basically the British equivalent to ASHRAE 12. The UK has had mitigation practices in place for a very long time. They also have standard monitoring practices, inspections and liabilities in place to address Legionella growth and Legionnaires’ Disease. We’re starting to see some of this implemented here in the US too, which is really good news.”
Lansing also notes it’s important to follow what is outlined in ASHRAE 188 as far as what buildings are considered high-risk. Spoilers: It’s not just healthcare. Multi-family residential buildings, as well as senior living facilities and buildings above 10 floors are all considered high-risk as well — something not everyone realizes.
“Increasing the domestic hot water circulation temperature is one of the key things for sure,” Lansing says when it comes to Legionella mitigation. “We need to be commissioning domestic hot water systems prior to occupancy for new buildings and also in existing buildings, ensuring the temperature is maintained above 120° F throughout the supply and return piping of the circulation system — and that number comes from ASHRAE 12. Once that is completed, it’s all about monitoring and maintaining those temperatures. Testing for Legionella is also key and has become much more accessible in recent years.
“Let’s take a look at Denmark for example,” he adds. “Denmark requires a minimum storage temperature of 140°F, and a minimum piping temperature of 122° F. Those numbers match what the UK uses identically. However, Denmark has more than 5 times the amount of Legionnaire's disease cases. Now, why is that? There are likely a lot of factors that contribute to this difference but without making any conclusive statements, but the domestic hot water design and maintenance is thought to be a core factor. A recent study from the Statens Serum Institute conducted an investigation of 104 buildings in Denmark and found that 66% of the buildings were operating below the minimum temperature requirement of 122° F, and 14% were operating below 113° F. Sampling and testing showed 40% of the buildings assessed contained Legionella counts above 10,000 CFU/L, well above the 1,000 CFU/L threshold where immediate action would be necessary. So regulation, monitoring and implementation are imperative because a standard is no good otherwise.”
John Mullen, director of technical services for IAPMO, notes that Legionella prevention methods in existing buildings may be different each time. However, the industry can focus on educating building operators on current best practices by helping them modify outdated standard operating procedures as it relates to building water systems.
“Performing in-depth reviews of normal building operating parameters on a regular basis allows building owners to keep a pulse on the efficacy of their programs,” Mullen explains. “By doing the hard work and performing program validation on a continuous basis, operations teams will feel more confident in their understanding when it comes to mitigating the risk or managing an outbreak.
Considering my time spent working in critical environments, I know very well that facilities operation teams have a lot on their plate. The resources available to building management teams are often severely stressed and tend to lack innovation because of that daily stress.
“If we can fix this gap with continuing education and provide resourceful platforms for discussing the perils of water management, we would all be better for it,” he adds. “Open sourcing information as it pertains of new investigatory tactics and common areas of neglect in critical environments will surely sharpen everyone’s swords.”
According to Fathers, the best way to eliminate Legionella bacteria is for facility managers to have a multi-barrier systems approach and water management plan.
“Its key facets include higher storage temperatures with ASSE 1017 thermostatic valve protection and proper distribution temperatures driven by legionella mitigation guidelines, with ASSE 1016/1069/1070 thermostatic valves at all points-of-use,” he says. “In addition, facility hot water management sanitation should include ultraviolet (UV) treatment, point-of-entry (POE) and point-of-use (POU) filtration, and treatment regimens like copper silver ionization, and chlorination. With the growing popularity of digital mixing stations – like IntelliStation – hot water purging and mitigation protocols can be met with ease. A digital mixing system can send highly-heated water out through distribution piping to all points-of-use. Typically this is accomplished in a facility in a very deliberate fashion, zone by zone, to assure thorough sanitization and safety of occupants.”
Pierre notes that Legionella bacteria enter buildings when — and if — the source water brings them to our door. “The rule of thumb is about half of large buildings will be colonized with Legionella bacteria. For example, our study on high-rise buildings in New York City showed only 54% (15/28) were colonized with Legionella. Once Legionella has colonized a building warm water system, there is no “silver bullet” or “one size fits all” to prevent the risk of Legionella.
“Implementation of a robust water safety and management plan and validating that plan with routine testing for Legionella is the best way to understand and manage the risk,” Pierre continues. “The control measures, corrective actions and mitigation methods in the water management plan should be evidence-based with publications or references showing efficacy against Legionella. One of the most important things to remember is that we don’t need to eradicate Legionella from our building water systems to reduce the risk of disease. Our goal is zero cases of disease, not necessarily zero Legionella. For a building with Legionella colonization, it can be virtually impossible to completely eliminate all Legionella, and thankfully, that unrealistic goal is not needed to reduce the risk of disease occurrence.”
Provided by Plumbing & Mechanical Engineer
Best Practices for Plumbing Design
There are several best practices for plumbing engineers to help prevent Legionella growth when designing new plumbing systems.
“Engineers should install ports throughout the water supply infrastructure to enable sampling and testing of the water to help better monitor the temperature and disinfectant levels,” notes Sigler. “Additionally, plans should incorporate double elbow fittings — such as Viega’s double drop elbow — to maintain proper water flow from either side of the plumbing loop. Furthermore, at a minimum, pipes should be installed with proper insulation in accordance with the 2021 IECC Section C404.4 for non-residential buildings and Section R403.5.3 for residential buildings.”
Sigler also points out that engineers should eliminate low-flow areas and minimize the distances between plumbing fixtures and hot water sources.
“In the International Plumbing Code (IPC), the maximum length for hot or tempered water piping must not exceed 50 feet from the source to the fixture,” he explains. “This helps reduce the possibility of bacteria growth while limiting the amount of energy needed to maintain water temperature.”
Another consideration to keep in mind, Sigler adds, is the distance between a building and water treatment plant. “The further a building is from the plant, there may be a need for a supplemental disinfectant system to ensure there is sufficient disinfectant residual throughout the water supply system.”
Fathers sees hot water recirculation as a critical weapon in battling Legionella.
“One thing to always look for and to eliminate are plumbing dead legs where warm, stagnant water can fester, serving as an ideal breeding grounds for legionella growth,” he says. “Also, it’s important to properly size all equipment in a safe and efficient plumbing design. Call it system optimization. This may entail a thorough inspection of a facility’s entire plumbing system — from the backflow device at entry to the water heater to distribution piping, and even sanitization of small aerators at all points of use — they often harbor bacteria.”
According to Mullen, the most common design decisions being made relating to Legionella prevention at present come in the form of automatic faucets and valves, with advanced scheduling tools that assist in flushing aged water.
“These components are typically associated with building maintenance systems and allow centralized control by building operators, whether onset or remote,” he explains. “Simple, yet often overlooked design enhancements include laminar flow aerators to help ease common areas of stagnation or considering tankless hot water storage with plate and frame heat exchangers in lieu of tank type.”
Mullen also notes that unfortunately, cost plays a large role in design decisions.
“Often, without the knowledge of these horror stories of legionella outbreaks, the wrong choices get made,” he says. “What is observed in the industry is that value engineering exercises early in the bidding process tend to scrap these new aged components from the design, which could lead to challenges in producing documentation if an outbreak were to occur. The barrier of entry on these components are slowly starting to come down, and this will, in turn, advance the popularity of installation leading to more data collection and interpretation.”
Additionally, tools such as IAPMO’s Water Demand Calculator are helping plumbing engineers design smarter, safer and more sustainable systems with smaller pipe diameters.
“For years, we’ve used pipe size in ways that do not represent the way we live today,” Mullen says. “With the increased popularity of digital meter faucets, water-conserving fixtures and intuitive building designs, we simply don't need the demand we once thought we did in various environments. The Water Demand Calculator includes a modern approach to designing water systems, based upon an updated probability of use.
This engineering tool is the most interesting advancement of plumbing design we've seen in decades. By engineering building systems with Legionella mitigation at the tip of the spear, professional engineers and certified plumbing designers can provide cost-effective solutions to their clients that do not require the additional cost of a broadband connection or dedicated power.”
Currently, the Water Demand Calculator is used for residential plumbing design; however, an updated version for commercial plumbing is currently in the works. Mullen is optimistic about getting the commercial version to the masses but notes it will be a laborious task and that more participation from industry professionals will be required. He encourages anyone interested in joining IAPMO's innovation task group to check out www.iapmo.org and consider attending the 2022 Water Demand Summit in November, to learn more.
Lansing also recommends limiting the diameter of water supply piping and the length of uncirculated branch piping to fixtures.
“For decades now, we’ve been installing low-flow fixtures with ‘high-flow’ piping,” he says. “When I say ‘high-flow’ piping, what I'm really referring to is oversized piping, which results in greater water stagnation and reduced water quality, and is generally understood to be a contributing factor in the rise of Legionnaires’ disease cases. To be honest, the industry was slow to pull together resources to develop an updated pipe sizing method. I don’t see that as the industry’s fault either. It has been a struggle to find the resources, both financial and human, to focus on advancing the efforts of Dr. Hunter’s work from 1940.
“When Hunter’s Curve went into widespread use, it was almost as the perception was that we had solved water pipe sizing forever and didn’t need to revisit this for at least 80 years,” he continues. “That’s obviously not the case, and there’s been discussion on revising Hunter’s Curve dating back decades. UPC Appendix M method, also known as the Water Demand Calculator, has done just that and it’s being used throughout the country now, with some states even including it within local plumbing codes. The next effort currently underway is extending the functionality beyond residential applications into commercial applications.”
Pierre believes the most common consideration for designing new plumbing systems is not necessarily specific products or components, but rather the compatibility of the components and materials with the facility’s water management plan.
“We should consider how the materials and components we select will impact water safety at the facility,” he explains. “Working with the water management team is essential to understanding these elements. For example: Are components and materials able to withstand high temperatures or chemical disinfection, if the plan includes these as corrective actions? If our water management plan includes sampling or monitoring of the hot water return, or storage tanks — has the design incorporated sampling ports or temperature gauges?”
What’s next?
So what’s next in terms of Legionella prevention and mitigation? Mullen notes that engineers should keep an eye out on the advancement in critical system automation and the use of artificial intelligence designed for the built environment.
“There’s a massive opportunity for data collection from these emerging technologies, and partnerships will be crucial to ensure that the information does not go to waste. The intellectual property extracted from these tools will undoubtedly be something we as an industry have a need for, considering the currency field data has in research and development. The more intelligent our buildings get, the more intuitive plumbing components and equipment will have to become to function in these ecosystem systems. If we don't continuously stay ahead of these innovations as engineers and installers, the adoption of these systems will see an unnecessary stifling effect. The industry is managing very well with the growing pains related to digitalization, and that makes me very hopeful.”
Fathers agrees that engineers will see greater value through evolving IoT technologies — especially in terms of how data can be interpreted and used.
“Some very surprising things are beginning to emerge as a result of the rich resources we’re finding with all this new data — call it ‘building profiling,’ he says. “Engineers, system designers, building owners and data analysts alike are finding it possible to learn so much more about the buildings in which we live and work — data that now allows us to better-design systems, fine-tune system performance, streamline or tailor maintenance schedules or more accurately size system components — even down to details like better sizing of mixing valves, precisely matched to their intended use.
“There’s always been a predisposition to oversize systems hot water systems, such as valves, pumps, etc., to ensure adequate hot water at all times,” Fathers adds. “But now, if data confirms that an average 300-bed hospital consumes a certain amount of domestic water, it allows facility designers to design building systems with far greater accuracy and efficiency.”
Sigler points to the use of treated wastewater inside of a building becoming more of a common practice.
“It is important to ensure that proper backflow protection is provided between potable and non-potable water sources as cross connections can introduce Legionella bacteria into the potable water supply system,” he explains. “Additionally, algae and bacteria growth patterns should be monitored at treatment facilities nationally.”
Lansing suggests engineers should produce more case studies going forward.
“If you’ve designed and implemented a system that addressed the issue of Legionella growth well, document what you did and get it out there as a case study,” he says. “It doesn’t have to be perfect. We need as much information as possible assessing the effectiveness of these strategies so we advance together as an industry. We need to be implementing measures, studying the effectiveness and then circling back and modifying the approaches accordingly. That's the only way to move forward without making arbitrary decisions that could impact other aspects of public health, like thermal injury, which may not appropriately address the risk of Legionnaire's disease. There are a lot of different standards and a lot of different risks, and it’s really important that we are taking all of them into context as we move forward with standard strategies.”
Pierre notes that engineers should look for the UPC and UMC to incorporate water management into its building and plumbing codes. “This will place a larger role on designers and engineers to consider Legionella and water management in the design phases. Additionally, the increased awareness could possibly lead to more legislation. At least six states have introduced legislation addressing the risk of Legionella in our building water systems, including the state where it all began — Pennsylvania.”
Based on findings from the Centers for Disease Control and Prevention, nine out of 10 cases of Legionnaires’ disease could be prevented with better water management. The Centers for Medicare & Medicaid Services goes even further. CMS now requires all hospitals, long-term care centers and skilled nursing homes to perform an environmental assessment, develop a water management program, and establish a sampling and monitoring strategy for their facilities. There are, however, no such consistent requirements for a health care facility’s water management program. Initial programs may only include a copy of the CDC toolkit for preventing Legionnaires’ disease, which is essentially filled in with basic information about the facility. Furthermore, the programs typically focus only on utility systems.
Current guidance, including the CMS requirements, requires health care facilities to focus on more water systems than just drinking water systems — and on pathogens other than Legionella. A 2019 study of non-Legionella infection risks published by the CDC showed that investigations of non-tuberculous mycobacteria (NTM) accounted for the greatest number of investigations (29.9%), followed by Pseudomonas spp. (18.7%) and Burkholderia spp. (10.4%).
Several possible exposure pathways and routes of transmission were identified, including contaminated sink drains, contaminated dialysis wall boxes, use of contaminated water in dental water lines, use of nonsterile water and inadequate disinfection of heater-cooler units used during cardiac surgery, water from contaminated showerheads and building water leaks in patient care areas. This demonstrates the need for facilities to establish procedures for maintaining their utility water systems, and including medical devices in their overall water management program. This requires a multidisciplinary team consisting of senior leadership, facility engineering, biomedical engineering, nursing and vendors.
The health care facility management team must work together to perform an environmental assessment of the entire facility, identifying areas of high risk due to patient populations and the presence of hazardous conditions. It is important to walk the facility and not rely on engineering drawings. The risk assessment and existing procedures, such as device manufacturer’s operating requirements, should be used to develop the water management program. The team must communicate regularly on the implementation of the program to ensure all actions are performed according to the established procedures. Documentation of these actions is essential to verify the program is being implemented as designed, and for the team to be able to review the effectiveness of the program on an ongoing basis.
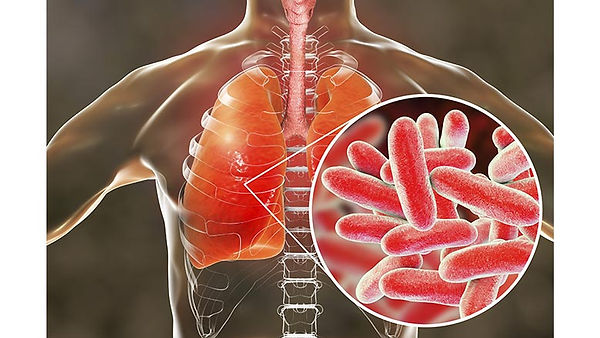



